Sister projects of HyInHeat
HyInHeat is just one the many European projects that focus on accelerating the transition to a more sustainable and decarbonized energy future. To create more visibility among our target audiences, we have started creating synergies between HyInHeat and other related projects.
Sister projects
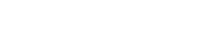
H2GLASS
H2GLASS is an EU-funded project. It is committed to accelerating decarbonisation in the glass industry by developing and applying the technology stack needed to realise full H2 combustion in glass production facilities. The consortium is made up of six Industrial Demonstrators representing major players of the glass and aluminium industries, along with a group of highly qualified industrial and research institutions. Together, they will develop, test and validate the H2GLASS technologies and demonstrate their transferability to other hard to abate industries.
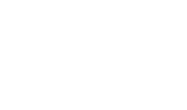
CESAREF
Refractory materials are an essential part of high-temperature industries including iron and steelmaking. They are made specifically to endure severe stress from production processes as well as various combinations of thermos-mechano-chemical damage mechanisms. Yet, the onset of a European move to net-zero emissions and digitalised processes is pushing them to adapt. The EU-funded CESAREF project, led by a team of steel, refractory and raw material producers and specialists, aims to make this a comfortable transition. To do this they will study and implement methods to improve energy efficiency and durability, efficiently utilise raw materials and enforce improved recycling, research microstructure designs for improved sustainability and prepare for the arrival of hydrogen steelmaking.
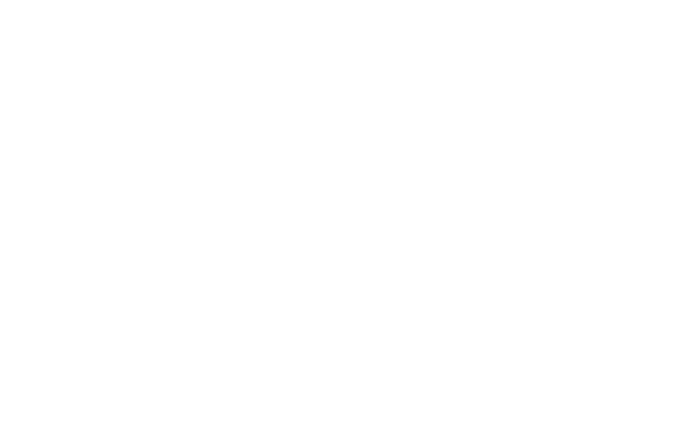
HyTecHeat
Steel production is an energy-intensive process that generates a significant environmental footprint. Although hydrogen technology is decarbonising upstream processes in Europe today, downstream processes still exclusively depend on natural gas during thermal treatment and reheating. The EU-funded HyTecHeat project aims to validate hybrid heating technologies based on natural gas with the progressive increase of hydrogen in downstream processing. It will create a prototype multifuel combustion system that will be tested in three pilot studies to achieve technology readiness level 7. It will also assess the resulting steel quality and determine optimal operating conditions to ensure that there are no defects in the final product.
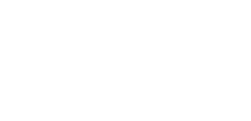
GreenHeatEAF
GreenHeatEAF develops and demonstrates the most important decarbonisation approaches at EAFs including the use of hydrogen to replace natural gas combustion in existing or re-vamped burners or innovative technologies like CoJet. Furthermore, decarbonisation of EAF steelmaking by solid materials like DRI/HBI and renewable carbon sources like biochar is tackled. Technologies to re-optimise the heating management with maximum heat recovery of off-gas and slag employing new sensor and soft-sensor concepts as well as extended digital twins are developed: as result the extended CFD and flowsheeting models, and monitoring and control tools will prognose the influences of the different decarbonisation measures on EAF and process chain to support upcoming decarbonisation investments and to enable the control of decarbonised hybrid heating with maximum energy efficiency.
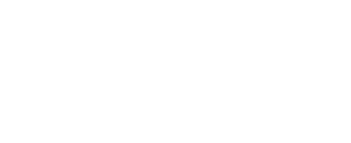
TWINGHY
TWINGHY will demonstrate an optimised heat transfer process based on hybrid burners in reheating furnaces, progressively decarbonising the reheating process through the increase of H2 in combination with O2 and by monitoring and controlling it through a digital twin. Two types of hybrid natural gas – hydrogen burners will be developed: one based on air and with the other one on oxy-combustion. They will be integrated into an operational industrial-scale reheating furnace demonstrator. To support that transition to hydrogen, a digital twin methodology will be developed and applied to the demonstrator and to a replication site. In parallel, a physics-based model will be created and validated on both sites too. The performances of both digital approaches will be compared. From the successful implementation of these actions, TWINGHY will contribute to the synergetic green and digitals transitions of the steel industry. It will allow to bring significant CO2 emission reductions while also saving energy and maintaining low NOx emissions.
FullH2ReHeat
The FullH2ReHeat project aims at investigating at semi-industrial scale the impact of H2 combustion in Reheating Furnace (RF). Especially, this project will focus on the so-called soaking zone, where the temperatures are the highest in the RF (atmosphere at ~1300°C), and where a modification of the atmosphere (~+15% increased moisture with H2 combustion) will impact the most the surface quality, internal soundness of products and mechanical properties. This project answers the 2nd Process Integration (PI) objective of this RFCS big ticket call. Especially, it will answer the sub-objective 2.5 with the use of the H2 carrier to efficiently transfer heat to semi-finished product, through optimized air-H2 novel burners developed by the partner.
HyDreams
HYDREAMS aims at total CO2 emissions reduction of 4.5 MtCO2/year by the partners by 2032. HYDREAMS will demonstrate clean H2 oxycombustion at TRL7 with minimal NOx emissions. The steel annealing furnace demonstrator will be supplied with the most OPEX-competitive and energy-efficient H2, which will use waste heat from the steel factory to produce CO2-free clean hydrogen at cost lower than 2 €/kg H2. The solutions’ competitive OPEX and CAPEX enable H2/O2 combustion to be cheaper than ‘business as usual’ natural gas/air combustion. Partners will demonstrate an increase in combustion energy efficiency by 10 to 47% with no loss in steel properties. They will contribute to ISO and CEN norms and obtain investment decisions for industrial-scale deployment in 5 steel plants and commitments from 8 brand-owners to adopt green steel in their products.